-
Audit
Durch unsere unabhängig und kompetent durchgeführten Prüfungsleistungen garantieren wir unseren Mandanten und deren Abschlussadressaten ein hohes Maß an Sicherheit und Vertrauen.
-
Assurance
Wir haben Assurance Service Lines im Bereich der prüfungsnahen Beratung etabliert, damit wir Sie bei der Identifizierung der für Sie relevanten Risiken und Herausforderungen unterstützen können.
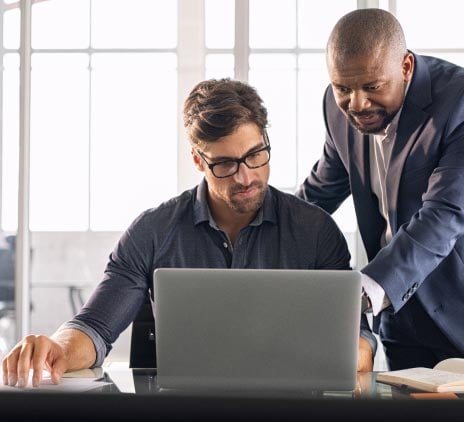
-
Technology Consulting
Erhalten Sie maßgeschneiderte Technologieberatung
-
Operational Excellence und Restrukturierung
Strategien für Erfolg und Stabilität
-
Deal Advisory
Problemlos Deals realisieren
-
Valuation & Economic and Dispute Advisory
Fachkompetenz für Ihre Fragestellungen
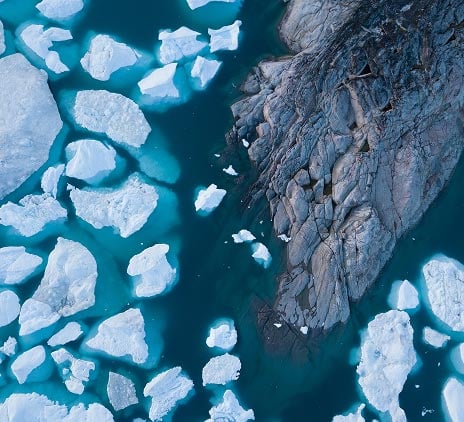
-
Unternehmen
Weil Ihr Unternehmen – ob national oder international – eine bessere Steuerberatung verdient.
-
Vermögende Privatkunden
Vermögen braucht Vertrauen, Transparenz und kluge Köpfe. Das können wir!
-
Finanzprozesse & Reporting
Unternehmensdaten messen und nutzbar machen
-
Immobilienwirtschaft
Beratung immobiliensteuerrechtlicher Spezialfragen
-
Finanzinstitute
Financial Services Tax – für Banken, Asset-Managements und Versicherungen
-
Tax im öffentlichen Sektor
Beratung und Services für die öffentliche Hand und Non-Profit-Organisationen
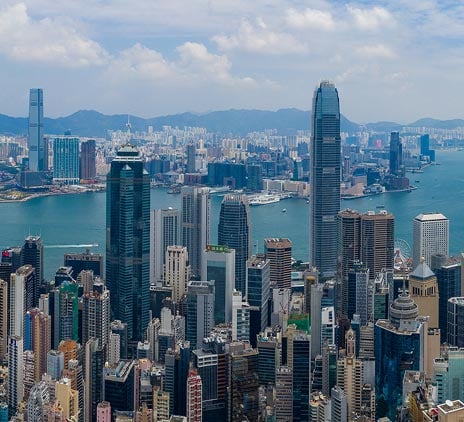
-
Arbeitsrecht
Vertretung für Unternehmen.
-
Commercial & Distribution
Einkauf und Vertrieb rechtssicher gestalten.
-
Compliance & Managerhaftung
Haftung für Ihr Unternehmen vermeiden.
-
Erben & Nachfolge
Überlassen Sie die Zukunft nicht dem Zufall.
-
Financial Services | Legal
Your Growth, Our Commitment.
-
Gesellschaftsrecht
Erfolgreiche Wirtschaftstätigkeit durch optimal gestaltete Gesellschaftsstrukturen.
-
Immobilienrecht
Alles über Immobilienwirtschaft, Hotellerie, Bau- und Architektenrecht, WEG und Mietrecht.
-
IT, IP & Datenschutz
IT-Sicherheit und digitale Innovationen.
-
Litigation | Dispute Resolution
Konflikte lösen.
-
Mergers & Acquisitions (M&A)
Ihr One-Stop-Dienstleister mit Fokus auf M&A-Transaktionen.
-
Restrukturierung & Insolvenz
Zukunft sichern in der Krise.
-
Energie, Telekommunikation und öffentliches Wirtschaftsrecht
Umfassende Beratung im Energierecht, Telekommunikationsrecht, öffentlichen Wirtschaftsrecht & regulierten Märkten.
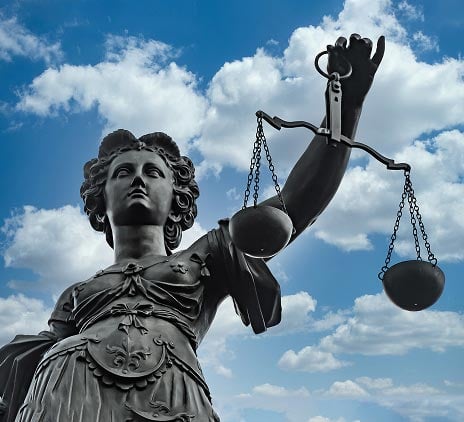
-
Technology Consulting
Digitalisierung gemeinsam meistern
-
IT Assurance
Sichere Informationen als Grundlage optimaler Analyse und Unternehmenssteuerung.
-
Tax Technology
Ihre Steuerabteilung – zukunftsfähig und leistungsstark!
-
IT, IP & Datenschutz
IT-Sicherheit und digitale Innovationen.
-
Öffentlicher Sektor
Digitalisierung, Prozesse & Projekte
-
Cyber Security
Beratung und Services für den Mittelstand in Deutschland
-
Sicherheitsberatung
Auch in stürmischen Zeiten den Kurs behalten
-
SAP Beratung & Projektmanagement
Wir halten Ihnen den Rücken frei – für ein erfolgreiches SAP-Projekt.
-
Data Engineering, Data Analytics und Künstliche Intelligenz
Datenbasierte Entscheidungen treffen und das Potenzial der Daten nutzen!
-
Sustainability Strategy
Den Grundstein für Nachhaltigkeit legen
-
Sustainability Management
Den nachhaltigen Wandel steuern
-
Sustainability Legal
Rechtliche Anforderungen an die nachhaltige Unternehmensführung
-
Sustainability Reporting
Nachhaltigkeitsperformance kommunizieren und Compliance sicherstellen
-
Sustainable Finance
Nachhaltigkeit in Investitionsentscheidungen integrieren
-
Grant Thornton B2B ESG-Studie
Grant Thornton B2B ESG-Studie
-
Expansion ins Ausland
Unsere Länderexpertise
-
Markteintritt in Deutschland
Ihr verlässlicher Partner
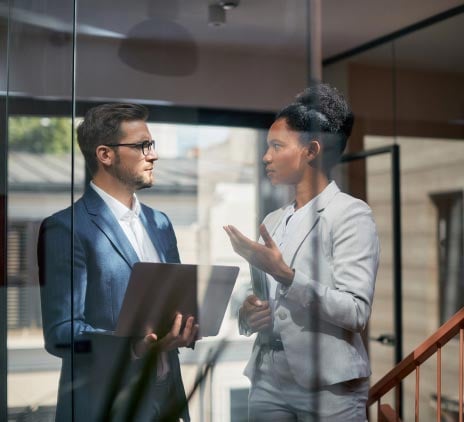
-
GRANT THORNTON OPINION in der ESG Automotive Nachhaltigkeitsthemen als Risiken und Chancen erkennenSenior Manager Dr. Stefan Hannen hat mit dem Magazin „Mobilität“, das als Beilage der Tageszeitung „Die Welt“ erscheint, über neue Geschäftsmodelle und aufkommende Reporting- und Kommunikationsverpflichtungen in der Automobilbranche gesprochen.
-
Pillar 2 Diskussionsentwurf für deutsches Umsetzungsgesetz liegt vorDie im Entwurf enthaltenen Regelungen sollen in einem eigenen neuen Gesetz „zur Gewährleistung einer globalen Mindestbesteuerung für Unternehmensgruppen“ verankert werden. Wir stellen die wichtigsten Punkte vor.
-
Rechnungslegung Auswirkungen der neuen US-GesetzgebungZwei von Präsident Joe Biden unterzeichnete Gesetze haben Auswirkungen auf den Zugang zum US-amerikanischen Markt für europäische Automobilhersteller. Deutsche Unternehmen mit geschäftlichen Beziehungen in die USA sollten insbesondere die bilanzielle Behandlung der gesetzlichen Neuerungen sorgfältig prüfen.
-
Interview Dynamic Dashboarding für Volvo Car GermanyWir haben gemeinsam mit Volvo Car Germany eine szenariobasierte und dynamische Dashboardlösung für den Finance Bereich bei dem Unternehmen entwickelt.
-
Sicherheitsberatung
Höchster Anspruch an Ihre Resilienz
-
Beratung für Stadtwerke und Kommunen
Expertise für eine nachhaltige Zukunft
-
Digitalisierung, Prozesse & Projekte
Spezialisiert auf den öffentlichen Sektor
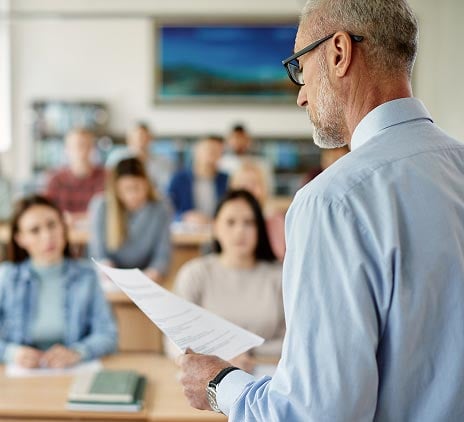
-
Work-Life-Balance
Starkes Engagement im Job und eine gute Work-Life-Balance kannst Du bei uns sehr gut kombinieren.
-
Entwicklung
Wir bieten Dir ein vielfältiges Portfolio und lebendiges Wachstum in einem starken Team. Deine Entwicklung ist unser Antrieb.
-
International Arbeiten
Unser internationales Netzwerk eröffnet Dir die Chance international zu arbeiten und interkulturelle Erfahrungen zu sammeln.
-
Diversity
Vielfalt ist Teil unserer DNA. Wir vereinen unterschiedlichste Fachrichtungen, Berufserfahrungen, Kulturen, Herkunftsländer, Altersgruppen und Geschlechter.
Ungeplante Produktionsausfälle als Kostentreiber
Ungeplante Anlagenstillstände gehören zu den größten Kostentreibern in der Produktion. In einigen Industrien liegen die Downtime-Kosten im Median bei über 100.000 Euro pro Stunde – jeder unvorhergesehene Ausfall kann also direkt sechs- bis siebenstellige Verluste verursachen. Traditionell setzten viele Hersteller auf reaktive Wartung („Run-to-Failure“) oder rein präventive Intervalle. Die Folgen einer reaktiven Instandhaltung sind jedoch gravierend: Organisationen, die hauptsächlich auf reaktive Wartung vertrauen, erleiden 3,3-mal mehr Ausfallzeit und produzieren bis zu 16-mal mehr Fehler/Defekte.*1 Präventive, zeitbasierte Wartung verringert zwar das Ausfallrisiko, ist aber oft ineffizient – Wartungen werden entweder zu früh (unnötiger Aufwand) oder zu spät (dennoch Störungen) durchgeführt.
Kein Wunder also, dass viele Betriebe bislang nicht optimal aufgestellt sind: Über 80 % der Betriebe halten nach wie vor an vorgeplanten Wartungsplänen fest, während nur rund 41 % Predictive Maintenance als primären Wartungsansatz etabliert haben. Lediglich 11 % der Unternehmen in Deutschland, Belgien und den Niederlanden verfügen bereits über einen so hoch entwickelten Reifegrad, dass sie angeben, vorausschauende Instandhaltung mit KI-gestützter Analyse zu nutzen. Die Implementierung gestaltet sich also in der Breite noch schwierig – u. a. wegen veralteter Maschinenparks, Datensilos und Mangel an Know-how im Bereich Analytics. Doch angesichts der aufgezeigten Risiken führt kein Weg daran vorbei, das Problem der ungeplanten Ausfälle aktiv anzugehen.
Predictive Maintenance und Condition Monitoring als technische Lösungsansätze
Die Antwort auf diese Herausforderung lautet Predictive Maintenance. Darunter versteht man einen datengetriebenen, proaktiven Wartungsansatz, der mittels Condition Monitoring (Zustandsüberwachung in Echtzeit) und Advanced Analytics potenzielle Probleme frühzeitig erkennt, bevor sie zum Stillstand führen. Moderne Fertigungsanlagen werden dazu mit einem Netz aus Sensoren (Temperatur, Vibration, Druck, Durchfluss etc.) und IoT-Geräten ausgerüstet, die laufend den Zustand kritischer Komponenten überwachen. Die gesammelten Maschinen- und Umgebungsdaten werden in einer IoT-Plattform oder Cloud zusammengeführt und durch Machine-Learning-Algorithmen analysiert. So lassen sich Muster identifizieren: Wann und unter welchen Bedingungen tritt ein bestimmter Verschleiß oder Fehler typischerweise auf?
Durch die Analysen der Daten können Unternehmen vorhersagen, wann eine Maschine mit hoher Wahrscheinlichkeit ausfallen wird. Anstatt also starre Wartungsintervalle einzuhalten, erfolgt die Instandhaltung zustandsbasiert: Nur wenn die Analysen anzeigen, dass eine Toleranzgrenze überschritten wird oder ein Anomalie-Muster einem bekannten Vorläufer eines Defekts entspricht, wird gezielt eingegriffen. Dies ermöglicht einen Paradigmenwechsel weg von reaktiven „Feuerwehr-Einsätzen“ hin zu planbarer, vorausschauender Wartung. Die Maschinen laufen länger unter optimalen Bedingungen, geplante Stillstände können mit der Produktion abgestimmt werden und Ersatzteile beziehungsweise Techniker stehen im Bedarfsfall rechtzeitig bereit.
Im Kontext von Industrie 4.0 gilt Predictive Maintenance als einer der vielversprechendsten Anwendungsfälle. Studien zeigen, dass über 70 % der Industrie-4.0-Vorreiter bereits auf Predictive-Maintenance-Lösungen setzen. Die benötigten Technologien – von vernetzten Sensoren (Industrial IoT) über Datenanalytik bis hin zu cloudbasierten Maintenance-Plattformen – sind heute ausgereift und zunehmend erschwinglich. Wichtig ist ein integrativer Ansatz: Die Daten aus der Instandhaltung sollten mit Produktions- und Qualitätsdaten verknüpft werden, sodass ein ganzheitliches Bild entsteht. Moderne MES-Systeme und Plattformen für das Asset Performance Management lassen sich entsprechend erweitern, um Predictive Maintenance als Baustein der digitalen Fertigung zu verankern.
Der wirtschaftliche Mehrwert in Zahlen und Fakten
Der wirtschaftliche Nutzen von Predictive Maintenance lässt sich durch konkrete Kennzahlen belegen. Eine Analyse von McKinsey ergab, dass vorausschauende Wartung Maschinenstillstände um 30-50 % reduzieren und die Lebensdauer von Anlagen um 20-40 % verlängern kann. Diese massive Senkung ungeplanter Ausfälle spiegelt sich direkt in höherer OEE (Overall Equipment Effectiveness) und niedrigem Investitionsbedarf (da Maschinen länger genutzt werden können) wider. BCG berichtet von Industrieprojekten, in denen nach Skalierung von Predictive Maintenance Programmen die ungeplanten Ausfallzeiten um 20-40 % sanken und die Total Cost of Ownership um etwa 10 % reduziert werden konnte – eine deutliche Kostenentlastung über den Lebenszyklus hinweg.
Auch im Instandhaltungsmanagement selbst zeigen sich Einsparungen. Laut einer Studie des US-Energieministeriums kann Predictive Maintenance rund 8-12 % gegenüber rein präventiver Wartung einsparen und sogar etwa 40 % gegenüber rein reaktiver Wartung. Statt teuren Notreparaturen und Folgeschäden wird in planbare, zustandsbasierte Eingriffe investiert. Zudem erhöht sich die Anlagenproduktivität. Wenn Maschinen störungsfrei laufen, steigt der Durchsatz.
Ausblick: Zukunft der vorausschauenden Instandhaltung
Mit Blick nach vorn ist klar: Predictive Maintenance entwickelt sich vom „Nice-to-have“ zum zentralen Pfeiler der Smart Factory. Die Fortschritte in KI und Machine Learning werden die Vorhersagegenauigkeit weiter erhöhen. In Zukunft könnten Algorithmen nicht nur Ausfälle vorhersagen, sondern als Prescriptive Maintenance auch gleich optimale Wartungsmaßnahmen vorschlagen. Erste Ansätze nutzen bereits generative KI, um Wartungstechnikern als digitaler Assistent zur Seite zu stehen und Reparaturabläufe zu optimieren.
Für Entscheider bedeutet dies: Sie sollten heute die Weichen stellen. Die globale Konkurrenz schläft nicht: Wer jetzt in digitale Fertigung und Predictive Maintenance investiert, kann seine Produktivität signifikant steigern und Ausfälle beherrschen – und damit einen entscheidenden Vorsprung im Markt erzielen. Die Technologie ist verfügbar und erprobt, die Use Cases existieren. Es gilt nun, ins Handeln zu kommen. Predictive Maintenance ist mehr als ein Buzzword – richtig umgesetzt, ist es ein mächtiger Hebel für effizientere, resilientere und zukunftsfähige Fertigung.
Jetzt handeln: Minimieren Sie Ausfallzeiten und maximieren Sie Ihre Produktivität!
Nutzen Sie das Potenzial von Predictive Maintenance, um ungeplante Stillstände zu vermeiden, Kosten zu senken und Ihre Anlagenleistung nachhaltig zu steigern. Lassen Sie sich von unseren Expert:innen beraten – gemeinsam entwickeln wir Ihre individuelle Instandhaltungsstrategie für die Smart Factory.
Der Artikel wurde in Zusammenarbeit mit Louis Yves Charles Punak (Consultant) verfasst.